Hybrid Digital Twins for Thermal Systems
Thermal System Efficiency is a Global Problem
Fouling in thermal systems is one of the most challenging, long-standing and costly problems the process industry faces today. In particular, fouling in heat exchanger networks leads to increased operating costs, maintenance issues, environmental impact of operations, and health & safety hazards.
ThermAI technology assists heat exchanger engineers, R&D specialists, and plant personnel to assess, predict and mitigate fouling in heat exchangers. ThermAI's proprietary technology was originally developed for the U.S. Navy and further developed in close collaboration with energy majors.
ThermAI Hybrid Twin™ – Accurate prediction of fouling in heat exchangers
ThermAI Data Studio™ is ThermAI's proprietary digital platform that uses Hybrid Digital Twin technology which integrates Artificial Intelligence with rigorous physics-based models and deep domain knowledge for advanced monitoring, predictive analytics and prescriptive maintenance of industrial thermal systems.
ThermAI Data Studio™ is used by refineries and petrochemical plants worldwide to increase production and energy efficiency, mitigate fouling, optimally manage cleaning of heat exchangers, reduce fuel consumption and CO2 emissions.

Under the Hood – Advanced Mathematical Models
At the core of ThermAI Studio™ is an advanced mathematical model based on models originally developed for the U.S. Navy, which enables calculating time-varying fouling rates as a function of local conditions in heat exchangers. The model accounts for the complex interactions between thermal and hydraulic phenomena and equipment geometry resulting in unprecedented accuracy. These deterministic models are coupled with Artificial Intelligence to boost accuracy and enhance capabilities.
Industry Deployment – Easy to Use Environment
ThermAI Data Studio™ is designed with a user-friendly flowsheet environment with state-of-the-art numerical solutions. The software platform provides a consistent, robust and flexible system for the solution of engineering heat transfer fouling problems at all stages of the engineering workflow - from R&D to operations support.
A key benefit of ThermAI Data Studio™ is the ability to run analysis, using consistent models and assumptions, the trade-offs between design activities and operational aspects. The software platform provides a unified framework that prevents the creation of “silos” between company functions allowing easy sharing of assumptions, validations and developments between R&D, engineering design, operations and operations support functions.
Technical features
1. Thermal and hydraulic model: accounts not just for the thermal impact of fouling but also for the increased pressure drops and possible reduction of throughput.
2. Tube-side fouling: A moving boundary approach is used to capture the growth of the fouling layer over time at any given point across the tube length, the corresponding reduction in cross–sectional flow area. A fouling rate model used in a distributed way, allows calculating the local value of fouling resistance at each point along the exchanger length as opposed to an average value for the whole exchanger.
3. Shell-side fouling: Effects of fouling in the shell-side is taken into account, including growth on the tube outer surfaces and occlusion of geometrical clearances.
4. Geometry: The heat exchanger configuration is accounted for (e.g. number of tube–side passes, tube diameter and length, baffle spacing, pitch arrangement, etc.).
5. Physical properties: The variation of physical properties with temperature and space for both shell–side and tube–side fluids is taken into account. Different thermo-physical property models/packages (including proprietary ones) can be used.
6. Aging of deposits: an aging model is implemented to describe the structural changes of the fouling deposit over time, hence its thermal conductivity.
Explore our Solutions:
Advanced Analytics: Fouling Propensity Analysis™
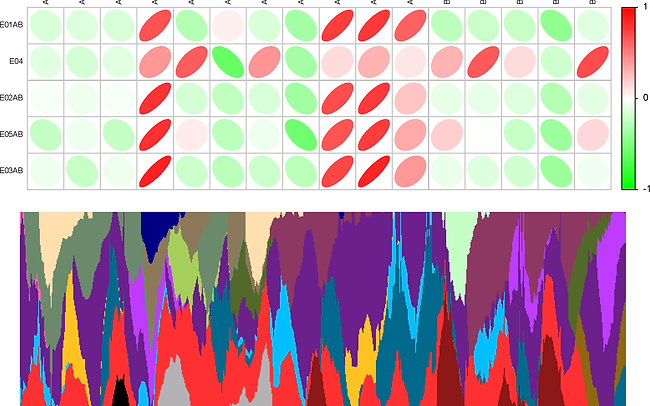
Advanced analytics to unveil key correlations between operating parameters, crude slates and fouling behaviour
Equipment Design: Dynamic Retrofit Test™

A predictive approach to test performance of a proposed retrofit design
Advanced Monitoring and Predictive Maintenance
